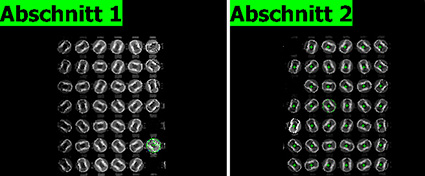
3D视觉抓件引导方案可以用来引导机器人分层抓取任意分布的工件。
例如,在一家汽车整车供应商,活塞由机器人自动从托盘上取下。活塞是分层堆叠在一起并且预先定位的。由于叠层存在高度差和中间层工件存在间隙,需要对每个单独的活塞进行3D 识别,以便引导机器人抓手拆卸。
我们采用基于IPC的视觉系统,可靠地解决了三维识别问题。
使用LMS400 time-of-flight扫描传感器,将它安装到抓手上,并由机器人在托盘上以恒定速度直线移动。如果传感器离托盘足够远,则可以一次扫描扫描整层工件,否则每层工件可以分成两个子区域进行拾取。每次图像采集时会同时获取已知位置的标定标记的图像信息,视觉系统使用这些标记直接将每个单独活塞的位置(X、Y、Z、Rz)输出到机器人坐标系中。
由于该系统可以处理距离图像信息,因此异物或倾斜的部件也会被检测为干扰轮廓。如果一个层是空的,中间层的位置将被确定,这样它也可以被系统自动移走,然后堆放在空托盘上。
视觉系统软件可以管理多种产品型号变体,这些变体型号可以很容易地输入到系统中。
At an automotive supplier, pistons are automatically removed from pallets by a robot. The pistons are roughly pre-oriented in forming films and are stacked on top of each other in several layers. Due to the stack height and the gap of the components in the intermediate layers, 3D recognition of each individual piston is required for removal with the gripper.
The 3D recognition was reliably solved with a PC-based vision system and the image processing software VisionTools V60.
The sensor used is an LMS400 time-of-flight scanner attached to the gripper, which is moved over the pallet by the robot at a constant speed and in a straight line. If the scanner is far enough from the pallet, the entire layer pad can be scanned with a single scan, otherwise the layer pad is picked up in two sections. For each image acquisition, calibration marks with a known position are also captured, which are used by the image processing system to output the position of each individual piston directly in the robot coordinate system (X, Y, Z, Rz).
Since the system works with distance images, foreign objects or tilted components are also detected as interfering contours. If a layer is empty, the position of the intermediate layer is determined so that it can also be automatically removed by the handling system and then stacked on an empty pallet.
The V60 image processing software manages several type variants that can be entered into the system with little effort.
The customer now has several such systems in use.