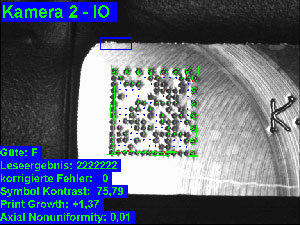
使用我们的视觉系统可以实现对于针刻码、激光码等各类码字的高可靠性读取。比如在某汽车项目中,气缸盖和曲轴箱加工生产线分别配备了矩阵代码读取装置。气缸盖的矩阵代码通过打针标记应用于机械加工的、从而反射的侧法兰表面。曲轴箱代码由激光打刻,该代码位于无光、未加工铸件表面的一侧。为了在曲轴箱上获得更均匀的表面和更高的对比度,在激光打码之前,用激光对打码区域进行平滑处理。机械加工过程会涂上一层油膜,这层油膜在钻孔乳化液和碎屑被吹走后仍然存在。
气缸盖生产线共有6个读取站,曲轴生产线共有8个读取站,可以通过视觉读取矩阵码。各个读取站分别位于加工单元前的互锁区域中。工件被输送到工位后停止,然后系统发送信号触发视觉系统进行读码。为了实现高可靠性读码,我们使用了外部光源进行照明,该光源作为独立单元与相机构成一体化的视觉系统。读取结果通过总线系统发送给输送控制系统。尽管读码条件非常困难,但我们的硬件和软件提供了非常可靠的读码结果,而且操作容易,集成难度很低。
Two production lines for machining cylinder heads and crankcases in the automotive industry were to be equipped with reading devices for matrix code reading. The matrix code of the cylinder heads is applied to a machined and thus reflective lateral flange surface by means of needle marking. The crankcases are marked by a lasered code, which sits on the side of the matt, unmachined casting surface. In order to achieve a more homogeneous surface and higher contrast on the crankcase, the marking area is smoothed with the laser before the code is applied. The machining process coats the engine parts with an oil film, which remains after the drilling emulsion and chips have been blown off.
With a total of 6 reading stations in the cylinder head production line and 8 reading stations in the crankshaft line, matrix code reading was possible. The individual reading stations are each integrated into the interlinking in front of a machining cell. For reading, the components are mechanically stopped in the concatenation and the reading is triggered via a system signal. In order to achieve the highest possible reading reliability, an external light source is used for illumination, which is supplied with the camera as a self-contained unit. The reading results are transmitted to the conveyor control system via a bus system. Despite difficult reading conditions, our hardware and software package provides reliable reading with low integration effort.