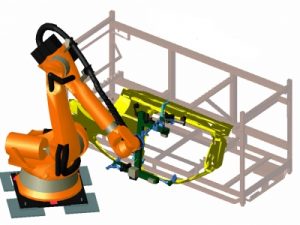
在车身生产过程中,机器人需要从料架中抓取车门、行李箱盖、侧部等各种零件。在这个过程中,为了正确拆卸部件,对机械公差提出了某些要求。如果工件位置发生了变化,则必须相应地校正机器人的移动。York的3D抓件引导系统演示了如何在自动化过程中快速、经济地完成这项工作。
使用我们的图像处理系统,可以得到工件的3D位置(6自由度),引导机器人实现正确抓件。相机和光源一般集成在抓手上(或机器人六轴上)。我们使用工件上的3~4个特征对视觉系统进行示教,然后视觉系统根据预先标定的数据及特征的变化,计算出工件的正确3D位置,并引导机器人进行定位。精度约为正负0.5 mm。
YORK的3D视觉引导系统消除了因零件滑动或容器放置不准确而引起的干扰。一套系统可用于多种型号的不同工件。如果更换了相机或改变了相机位置,可以通过自动校准实现快速恢复。
In car body construction, various parts such as doors, trunk lids, side parts etc. are removed from specially manufactured containers. In this process, certain requirements are placed on the mechanical tolerances in order to remove the components correctly. If the component position changes, the robot movement must be corrected accordingly. A 3D image processing system in an automobile manufacturer's joining and welding line demonstrates how this can be done quickly and economically in an automatic process.
Using an image processing system, the removal position of side frames in special containers is dynamically adapted to the current three-dimensional position (6 degrees of freedom) of the component. The standard cameras and lighting are integrated in the gripper. Three unique features are required on the component, which are taught in with the aid of an adjustment function and then used for localization. Each of the features can move in a search window of approx. 100 x 100 x 100 mm. The new component position is calculated from the calibration data and the two-dimensional features and transferred to the robot. An accuracy of approx. +/- 0.5 mm is achieved.
Disturbances caused by slipped parts or inaccurately placed containers are eliminated. The system can be used for a large number of very different parts. A concrete application can be realised by a mechanical engineering company alone using the guideline. No special calibration bodies are required for the system. The cameras are calibrated fully automatically on a real component, complex calculations or measurements are not necessary for the system integrator. If the camera is replaced or the position is changed, only a menu-guided rough adjustment of the cameras with subsequent automatic calibration run is required.